Hoe kies je meestal een extruder? U moet niet alleen uw eigen behoeften analyseren, maar u moet ook uw leveranciers en extruders volledig begrijpen.
Bedrijven hebben een basiskennis van de vraag of ze een dubbelschroefs- of een enkelschroefsextruder moeten kopen voordat ze een nieuwe extruder kopen. Wat voor soort materialen moeten er geproduceerd worden? Afhankelijk van de productspecificaties is de hoeveelheid gebruikt materiaal verschillend. U kunt de "Schroefdiameter en product" Specificatiegrootte raadplegen, de diameter van de schroef selecteren en vervolgens de specificaties van de extruder verder selecteren op basis van de diameter van de schroef.
Bedrijven hebben een basiskennis van de vraag of ze een dubbelschroefs- of een enkelschroefsextruder moeten kopen voordat ze een nieuwe extruder kopen. Wat voor soort materialen moeten er geproduceerd worden? Afhankelijk van de productspecificaties is de hoeveelheid gebruikt materiaal verschillend. U kunt de "Schroefdiameter en product" Specificatiegrootte raadplegen, de diameter van de schroef selecteren en vervolgens de specificaties van de extruder verder selecteren op basis van de diameter van de schroef.
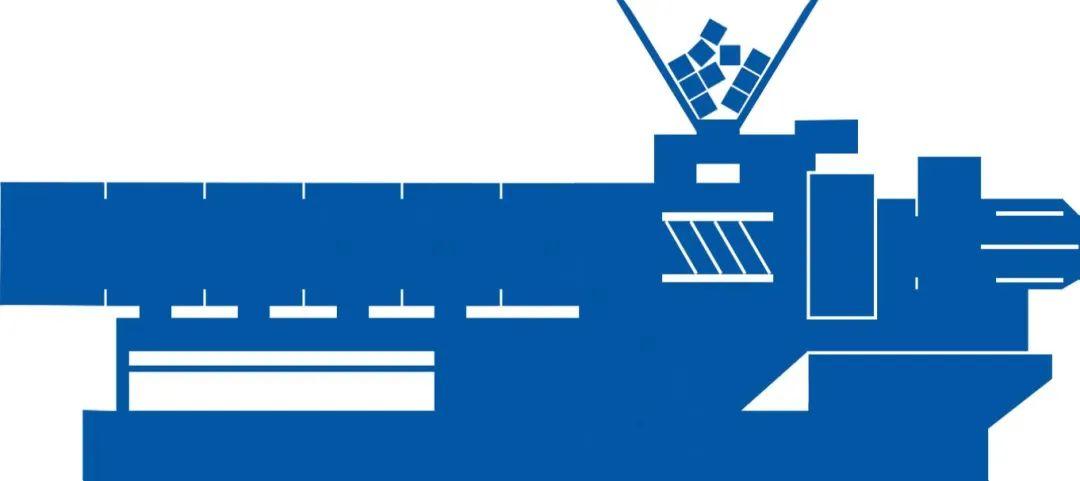
Nadat het type en de specificatie van de extruder zijn bepaald, is het vinden van de fabrikant van de apparatuur ook een probleem waar aandacht aan moet worden besteed. Om nog maar te zwijgen van buitenlandse merken: veel binnenlandse extruderbedrijven bestaan al heel lang, zijn krachtig en hebben vele jaren praktische ervaring. kunt u kiezen uit meerdere perspectieven, zoals productkwaliteit en after-sales service.
Schroef snelheid
Dit is de kritische factor die de productiecapaciteit van een extruder beïnvloedt. De schroefsnelheid is niet alleen bedoeld om de extrusiesnelheid en het extrusievolume van het materiaal te verhogen, maar nog belangrijker, om de extruder in staat te stellen een hoge output te bereiken en tegelijkertijd goede weekmakende effecten te bereiken.
Schroef snelheid
Dit is de kritische factor die de productiecapaciteit van een extruder beïnvloedt. De schroefsnelheid is niet alleen bedoeld om de extrusiesnelheid en het extrusievolume van het materiaal te verhogen, maar nog belangrijker, om de extruder in staat te stellen een hoge output te bereiken en tegelijkertijd goede weekmakende effecten te bereiken.
In het verleden was het vergroten van de schroefdiameter de belangrijkste manier om de output van extruders te vergroten. Hoewel de schroefdiameter toeneemt, zal het per tijdseenheid geëxtrudeerde materiaal toenemen. Maar een extruder is geen schroeftransporteur. Naast het extruderen van materialen extrudeert, roert en knipt de schroef ook het plastic om het week te maken. Onder de veronderstelling dat de schroefsnelheid onveranderd blijft, is het meng- en afschuifeffect van een schroef met een grote diameter en een grote groef op het materiaal niet zo goed als dat van een schroef met een kleine diameter.
Daarom vergroten moderne extruders de productiecapaciteit voornamelijk door de schroefsnelheid te verhogen. De schroefsnelheid van een gewone extruder is 60 tot 90 rpm (per minuut, hetzelfde hieronder) voor een traditionele extruder. Nu is het over het algemeen verhoogd tot 100 ~ 120 tpm. De extruder met hogere snelheid bereikt 150 tot 180 tpm.
Als de schroefdiameter ongewijzigd blijft en de schroefsnelheid wordt verhoogd, zal het koppel dat de schroef ondergaat toenemen. Wanneer het koppel een bepaald niveau bereikt, bestaat het gevaar dat de schroef wordt gedraaid. Door het materiaal en het productieproces van de schroef te verbeteren, de schroefstructuur rationeel te ontwerpen, de lengte van het invoergedeelte in te korten, de stroomsnelheid van het materiaal te verhogen en de extrusieweerstand te verminderen, kan het koppel worden verminderd en kan het lager van de schroef worden verminderd. capaciteit kan worden verbeterd. Hoe je een redelijke schroef kunt ontwerpen en de schroefsnelheid kunt maximaliseren onder de veronderstelling dat de schroef hiertegen bestand is, vereist dat professionals deze door een groot aantal experimenten verkrijgen.
Schroef structuur
De schroefstructuur is de belangrijkste factor die de output van de extruder beïnvloedt. Zonder een redelijke schroefstructuur is het simpelweg verhogen van de schroefsnelheid om het extrusievolume te vergroten in strijd met objectieve wetten en zal dit geen succes hebben.
Het ontwerp van de snelle en efficiënte schroef is gebaseerd op een hoge rotatiesnelheid. Het weekmakende effect van dit soort schroeven zal slechter zijn bij een lage rotatiesnelheid, maar het weekmakende effect zal geleidelijk verbeteren nadat de rotatiesnelheid van de schroef wordt verhoogd, en het effect zal worden verkregen wanneer de ontwerprotatiesnelheid wordt bereikt. Op dit moment kunnen zowel een hoge productiecapaciteit als een gekwalificeerd weekmakend effect worden bereikt.
Vat structuur
De verbetering van de tonconstructie betreft vooral het verbeteren van de temperatuurbeheersing van de voersectie en het opzetten van een voergoot. De gehele lengte van dit onafhankelijke voergedeelte is een watermantel en er worden geavanceerde elektronische regelapparatuur gebruikt om de temperatuur van de watermantel te regelen.
Of de temperatuur van de watermantel redelijk is, is van groot belang voor de stabiele werking van de extruder en efficiënte extrusie. Als de watermanteltemperatuur te hoog is, zal de grondstof voortijdig zacht worden en zal zelfs het oppervlak van de grondstofdeeltjes smelten, wat de wrijving tussen de grondstof en de binnenwand van het vat zal verzwakken, waardoor de extrusiekracht wordt verminderd en extrusievolume. De temperatuur mag echter niet te laag zijn. Een vat met een te lage temperatuur zal ervoor zorgen dat de rotatieweerstand van de schroef te groot is. Wanneer het draagvermogen van de motor wordt overschreden, zal dit problemen veroorzaken bij het starten van de motor of zal de snelheid onstabiel worden. Geavanceerde sensoren en besturingstechnologie worden gebruikt om de watermantel van de extruder te bewaken en te regelen, waardoor de watermanteltemperatuur automatisch binnen het procesparameterbereik wordt geregeld.
Reductiemiddel
Onder de veronderstelling dat de structuur hetzelfde is, zijn de vervaardigingskosten van het verloopstuk ruwweg evenredig met de totale omvang en het gewicht ervan. Omdat de vorm en het gewicht van het verloopstuk groot zijn, betekent dit dat er tijdens de productie veel materialen worden verbruikt, en dat de gebruikte lagers ook relatief groot zijn, wat de productiekosten verhoogt.
Voor extruders met dezelfde schroefdiameter verbruiken snelle en efficiënte extruders meer energie dan conventionele extruders. Het is noodzakelijk om het motorvermogen te verdubbelen en de framegrootte van het verloopstuk dienovereenkomstig te vergroten. Maar een hoge schroefsnelheid betekent een lage reductieverhouding. Voor reductoren van dezelfde grootte is de tandwielmodule met een lage overbrengingsverhouding groter dan die met een grote overbrengingsverhouding, en wordt ook het draagvermogen van de reductor vergroot. Daarom is de toename van het volume en het gewicht van het reductiemiddel niet lineair evenredig met de toename van het motorvermogen. Als u het extrusievolume als noemer gebruikt en dit deelt door het gewicht van het verloopstuk, zal het getal kleiner zijn voor een snelle en efficiënte extruder en groter voor een gewone extruder.
In termen van eenheidsoutput is het motorvermogen van een hogesnelheids- en hoogefficiënte extruder klein en het gewicht van het reductiemiddel klein, wat betekent dat de machineproductiekosten per eenheid output van een hogesnelheids- en hoogrenderende extruder is lager dan die van een gewone extruder.
motorisch aangedreven
Voor extruders met dezelfde schroefdiameter verbruiken snelle en efficiënte extruders meer energie dan conventionele extruders, dus het is noodzakelijk om het motorvermogen te vergroten. Een hogesnelheidsextruder van 65 mm heeft een motor van 55 kW tot 75 kW nodig. Een hogesnelheidsextruder van 75 mm heeft een motor van 90 kW tot 100 kW nodig. Een hogesnelheidsextruder van 90 mm heeft een motor van 150 kW tot 200 kW nodig. Dit is één tot twee keer groter dan het motorvermogen van gewone extruders.
Tijdens normaal gebruik van de extruder werken het motortransmissiesysteem en het verwarmings- en koelsysteem altijd. Het energieverbruik van transmissieonderdelen zoals motoren en reductiekasten is verantwoordelijk voor 77% van het energieverbruik van de gehele machine; verwarming en koeling zijn goed voor 22,8% van het input-energieverbruik van de gehele machine; instrumentatie en elektriciteit goed voor 0,8%.
Extruders met dezelfde schroefdiameter zijn uitgerust met grotere motoren, die meer elektriciteit lijken te verbruiken. In termen van output zijn snelle en efficiënte extruders echter energiebesparender dan conventionele extruders. Een gewone extruder van 90 mm heeft bijvoorbeeld een motor van 75 kW en een productiecapaciteit van 180 kg. Elke kilogram geëxtrudeerd materiaal verbruikt 0,42 kilowattuur elektriciteit. Een snelle en efficiënte 90-extruder heeft een productiecapaciteit van 600 kilogram en een motor van 150 kilowatt. Elke kilogram geëxtrudeerd materiaal verbruikt slechts 0,25 kilowattuur elektriciteit. Het energieverbruik per extrusie-eenheid bedraagt slechts 60% van eerstgenoemde. Het energiebesparende effect is opmerkelijk. Hiermee wordt alleen het energieverbruik van de motor vergeleken. Als rekening wordt gehouden met het stroomverbruik van de verwarming en ventilator op de extruder, zal het verschil in energieverbruik nog groter zijn. Extruders met grote schroefdiameters moeten worden uitgerust met grotere verwarmingselementen en het warmtedissipatiegebied neemt ook toe. Daarom is voor twee extruders met dezelfde productiecapaciteit de cilinder van de nieuwe hogesnelheids- en hoogefficiënte extruder kleiner en verbruikt de verwarmer minder energie dan de traditionele extruder met grote schroef, wat ook veel elektriciteit bespaart bij verwarming .
In termen van verwarmingsvermogen verhogen snelle en efficiënte extruders, vergeleken met gewone extruders met dezelfde schroefdiameter, het verwarmingsvermogen niet vanwege de grotere productiecapaciteit. Omdat de verwarmer van de extruder elektriciteit verbruikt, voornamelijk in de voorverwarmingsfase. Tijdens normale productie wordt de hitte van het smelten van materiaal voornamelijk omgezet door elektrische energie van de motor te verbruiken. De geleidbaarheid van de verwarmer is erg laag en het elektriciteitsverbruik is niet erg hoog. groot. Dit is duidelijker bij hogesnelheidsextruders.
Toen frequentieomvormertechnologie nog niet op grote schaal werd gebruikt, gebruikten traditionele extruders met een groot vermogen over het algemeen gelijkstroommotoren en gelijkstroommotorcontrollers. In het verleden werd algemeen aangenomen dat DC-motoren betere vermogenskarakteristieken hebben dan AC-motoren, een groter snelheidsbereik hebben en stabieler zijn bij lage snelheden. Bovendien zijn frequentieomvormers met een hoog vermogen relatief duur, wat ook de toepassing van frequentieomvormers beperkt.
De afgelopen jaren heeft de invertertechnologie zich snel ontwikkeld. Vector-type omvormers realiseren een sensorloze regeling van het motortoerental en koppel. De laagfrequente eigenschappen hebben grote vooruitgang geboekt en ook de prijs is relatief snel gedaald. Vergeleken met DC-motorcontrollers is het grootste voordeel van frequentieomvormers de energiebesparing. Het maakt het energieverbruik proportioneel aan de motorbelasting. Wanneer de belasting zwaar is, neemt het energieverbruik toe, en wanneer de motorbelasting afneemt, wordt het energieverbruik automatisch verlaagd. De energiebesparende voordelen bij langdurige toepassingen zijn zeer aanzienlijk.
Maatregelen om trillingen te verminderen
Hogesnelheidsextruders zijn gevoelig voor trillingen en overmatige trillingen zijn zeer schadelijk voor het normale gebruik van de apparatuur en de levensduur van de machineonderdelen. Daarom moeten er meerdere maatregelen worden genomen om de trillingen van de extruder te verminderen om de levensduur van de apparatuur te verlengen.
De onderdelen van de extruder die gevoelig zijn voor trillingen zijn de motoras en de hogesnelheidsas van het verloopstuk. De hogesnelheidsextruder moet zijn uitgerust met een motor en reductiemiddel van hoge kwaliteit om te voorkomen dat hij een bron van trillingen wordt als gevolg van de trillingen van de motorrotor en de hogesnelheidsas van het reductiemiddel. De tweede is het ontwerpen van een goed transmissiesysteem. Aandacht besteden aan het verbeteren van de stijfheid, het gewicht en de kwaliteit van alle aspecten van de verwerking en montage van het frame is ook een belangrijke stap in het verminderen van de trillingen van de extruder. Een goede extruder hoeft tijdens gebruik niet met ankerbouten te worden vastgezet en er is geen trilling. Dit is afhankelijk van het feit of het frame voldoende stijfheid en eigen gewicht heeft. Bovendien moet de kwaliteitscontrole van de verwerking en assemblage van elk onderdeel worden versterkt. Controleer tijdens de verwerking bijvoorbeeld de parallelliteit van de bovenste en onderste vlakken van het frame, de loodrechtheid van het montageoppervlak van het verloopstuk en het vlak van het frame, enz. Meet tijdens de montage zorgvuldig de ashoogten van de motor en het verloopstuk, en Bereid de verloopstukken strikt voor om de motoras en de ingaande as van het verloopstuk concentrisch te maken. En maak het installatieoppervlak van het verloopstuk loodrecht op het vlak van het frame.
Instrumentatie
De extrusieproductie is een zwarte doos en de situatie daarbinnen is helemaal niet te zien. Het kan alleen worden weerspiegeld door instrumenten en meters. Daarom zullen nauwkeurige, intelligente en eenvoudig te bedienen instrumenten ons in staat stellen de interne omstandigheden ervan beter te begrijpen, zodat de productie snellere en betere resultaten kan bereiken.
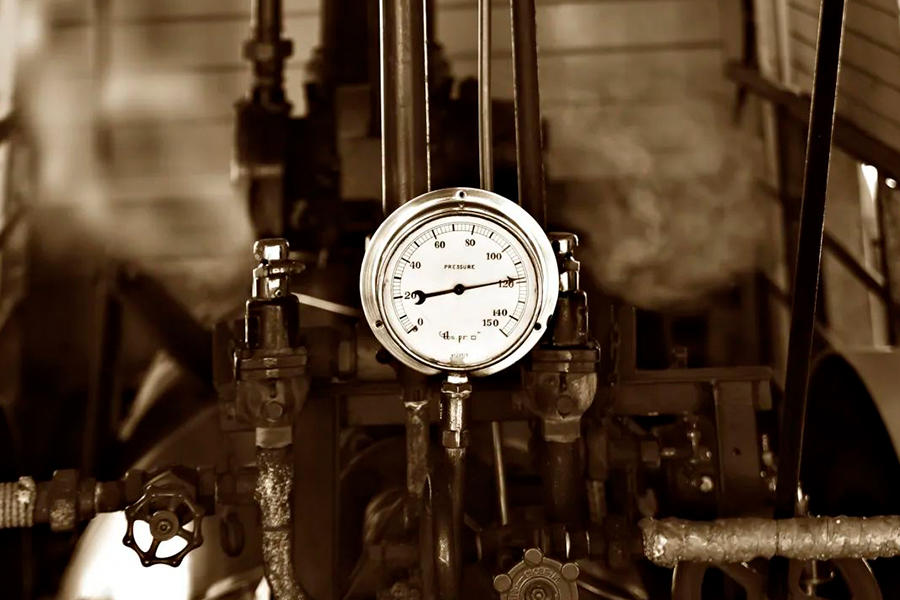